Panel designs in 3D:
How the digital twin simplifies your control cabinet designs and production
Digital twin: Does this make you think of a 3D model as a practical orientation for panel building? Or instead as a vision of the future for digital transformation? With standardised schematic creation as a foundation, control cabinet designs in 3D are also in reach for your company. Venture closer to the factory floor with EPLAN. Your colleagues in production will thank you just as much as your clients!
Where is your panel building heading?
Let’s take this journey together!
Different worlds? Electrical designing in the office and panel building on the factory floor
As an engineer, do you always have an eye on how your colleagues on the factory floor are making your designs a reality? Two-dimensional schematics can naturally be used to equip and cable control cabinets. But some of the needed information is still missing: Where exactly do components and bore holes need to be placed on the mounting plate? And the operating elements on the door? Where should the cable ducts, DIN rails and terminals be installed? If there aren’t any exact specifications, various queries from the production team and the client are inevitable. An acute shortage of skilled workers also has negative effect on production and delivery schedules. Is there anything you can do about this in electrical design?
2D schematics vs 3D designs: comparing panel production
There definitely is! Using data from the schematics created in EPLAN, you can firstly compile important information for materials procurement. Secondly, the EPLAN project data is the perfect foundation for deriving a realistic digital twin of the planned control cabinet. The right 3D software makes it easier for electrical engineers when designing the control panel and for technicians when producing it.
Panel building with 2D schematics
- Where exactly are the components placed in the control cabinet? Does it all fit?
- No information about where cable ducts or bore holes should be placed
- Assembly and cabling can only be realised by experienced employees
- Every finished control cabinet looks different, despite being produced in series
⇒ Queries, re-working and a lack of personnel waste both time and precious resources
Panel building with a 3D model
- All components are already positioned on the mounting plate and displayed realistically
- The entire structure of the control cabinet is clearly described
- Understandable visualisations for coordination and project approvals
- Production assistance tools can guide even inexperienced workers through mounting and wiring
⇒ Virtual prototype for fast panel building and smooth approval processes
Four advantages of virtual prototyping for panel building

Virtual prototyping can give companies decisive advantages, ensuring better collaboration between engineering, panel building and other downstream processes. Here we present four important advantages for using virtual prototypes for your processes in control cabinet engineering and construction. Download it for free now!
EPLAN in Practice
Find out how companies are using our solutions to meet current technical development challenges and improve their bottom line.
Using EPLAN Software to create the digital twin for your panel building
There’s still a lot to do after creating the schematics. EPLAN provides you the software for the 3D designs of your control and switchgear systems. EPLAN also gets used on the production floor to simplify control cabinet manufacturing based on the digital twin.

Do you have challenges in engineering and manufacturing of machines?
Discover your possibilities with EPLAN in mechanical engineering as well. Learn more about automated engineering and machine wiring.
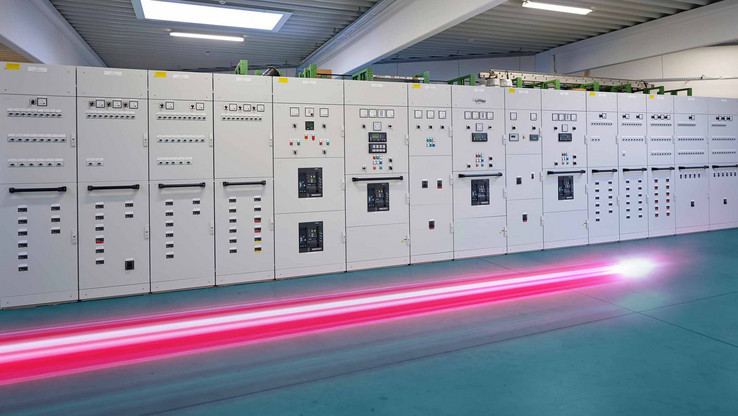
Efficient production of copper busbars
The detailed 3D model with mechanical enclosure structure, electrical devices and copper busbars provides a 100 percent digital description of the entire switchgear. Three-dimensional planning offers decisive added value, particularly regarding the copper busbars: It prevents the production of busbars that do not fit. Unnecessary costs are thus reduced.