At electromobility’s sweet spot
Voltabox is a major driver of the electric mobility trend
E-Mobility is the topic of the hour. All global mobility is on the threshold of a new era. Modern lithium-ion battery systems are increasingly replacing conventional drives. Before a vehicle can be electrified, however, numerous questions have to be answered: What capacity can be accommodated in a given installation space? What voltage is required for the application? This calls for in-depth know-how.
Voltabox AG, located in Delbrück, Germany, which specialises in the development and manufacture of lithium-ion battery systems, is operating in the centre of this trend-theme. To ensure that the battery system as a key component of electrically powered vehicles can be designed as precisely as possible to the conditions and requirements of the respective application, Voltabox fully exploits the automation potential in cable and wire harness design with EPLAN Harness proD during battery development. Voltabox’s Team Leader for Battery System Development, Christopher Bern, explains: “We’ve discovered that no other tool can be learned as quickly and is so intuitive to use as Harness, and the connection between Electric P8 and Harness offers so many advantages that we wouldn’t want to do without it.”
Sweet spot: in the middle of the value chain
Voltabox sees itself in the sweet spot of electromobility – exactly in the middle of the value chain with its battery systems. The company has three divisions. The Voltapower division offers customer-specific battery systems for industrial applications, e.g. forklifts, mining vehicles, trolley buses and automated guided vehicles. The second division is Voltaforce, specialising in lithium-ion batteries for the mass market. The focus here is on starter bat- teries for motorcycles and sports cars plus battery packs for pedelecs and e-bikes. The third and final division is Voltamotion, which concentrates on the development of electric drive systems: parts needed for the electrification of drivetrains. These components are brought to market at the company’s in-house development centre in Aachen, such as the power electronics for complete electrification of high-performance vehicles, including highly efficient electric motors.
Voltage guaranteed – battery development
Christopher Bern doesn’t mince words when it comes to the challenging field of activity experienced by the Voltabox engineers: “We have to develop customer-specific solutions as quickly as possible. Initial prototypes should already be ready for serial production.” Yet prototypes and small batch sizes must be realised in a cost-efficient manner and adaptations must be quick and easy to implement at any time. And this isn’t a choice, it’s a must if you want to play a leading role in one of the world’s most dynamic industries: “We demand the highest quality from ourselves and our premium products. It’s the only logi- cal conclusion when two market leaders work together.” One is Voltabox and the other is EPLAN, which provides the solutions that make automation and workflow collabora- tion possible in the first place: EPLAN Electric P8 for electrical engineering, and EPLAN Harness proD for cable and wire harness design in 2D and 3D. A look into the battery development process at Voltabox highlights the how and why.
Featuring Voltabox’s development process
There are four work steps that can be outlined in the battery development process: the 3D layout space survey and schematic design, component placement and 3D wire harness development, prototype production and manufacturing enquiries plus documentation. Voltabox is interested in quickly achieving first-class results – which can’t be done with a sequential workflow of isolated departments and insular solutions. Even while a Voltabox client is providing information about the layout space and mechanical design data for the target application, the schematic concept is already being designed in parallel.
Both of these data packages are imported into EPLAN Harness proD, and “then the component placement can get started,” Bern says. “Wiring pathways are defined and networked according to the schematic. Then individual assemblies are gradually created.” In addition to the high-voltage wiring of multiple battery containers, the external wiring of a battery system often includes communication with the central controlling device, which ensures reliable battery operation and functions as the interface between the battery and vehicle.
The generated assemblies can be exported and fed back into the mechanical engineering design in order to make appropriate changes and to take development cycles into account. This is easy because EPLAN Harness proD is open to MCAD systems and can easily be integrated into existing system landscapes. The prototype production department, with all the necessary information from EPLAN Harness proD – the wire harness, the bill of materials of all the required components, the surface protection chart, etc. – can subsequently produce first samples; wire drawings and nail boards are derived in parallel to start manufacturing enquiries. EPLAN Harness proD automatically puts together all the documentation, including the nail board and wire drawings. As Bern explains, “Operating instructions, assembly documentation for manufacturing and visualisations – easily understood by anyone – are indispensable. There was nothing like this back at the beginning.”
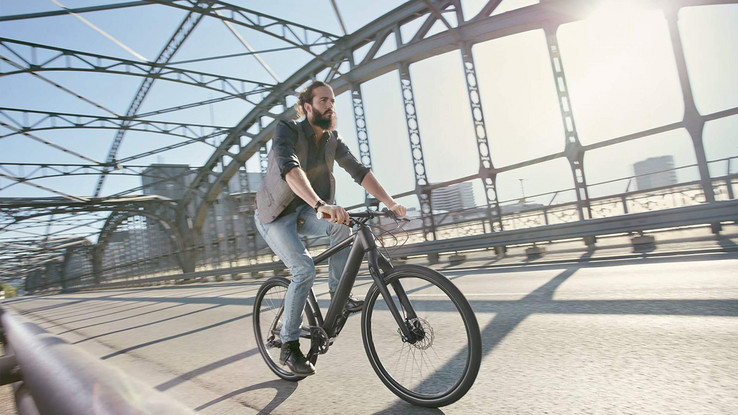
Customer-specific battery systems are used, for example, in e-bikes and pedelecs.
Image: Voltabox AG
The Point-and-Click principle takes hold
The requirements analysis by Voltabox first leads to the selection of the ideal battery cell, for which the suitable wiring of appropriate modules is then designed. The system concept is developed together with the mechanical engineering design and checked against the data for the target application. Bern: “This is about the available layout space and also whether the handling concept is suitable or if the fastening points are accessible.” The selection and placement of sub-components and wires is done via the Harness library, a component database that Voltabox itself created and that includes accessories such as blanking plugs and cavity seals. The point-and-click principle takes hold: “We can place everything in the layout space with just a few clicks; the wiring for the power and communication units can be realised very quickly,” Bern says. Explicitly addressing not just the interaction with the mechanical design, but also the interplay between electrical project planning and wire harness design, he adds, “The Harness interface to Electric P8 is a huge advantage, making life much easier for the designer. We can automatically import the networking plans.”
Moreover, the derivations of assembly drawings can be truly efficient, with the changes automatically imported, i.e. updated, and enriched with additional information. The key is interaction: The comprehensive export interface between MCAD and ECAD enables faster development cycles for creating the battery system’s digital twin. The mechanical design can import wire harnesses and positioned components back into its system and adjust their design accordingly – for instance for fasteners and cut-outs – to safely incorporate the harnesses into the battery system.
Cooperation between the individual development departments at Voltabox lies at the heart of an efficient development process. The company is achieving an even higher level of integration with the upcoming connection of EPLAN Harness proD to its PDM system, which is going to be implemented with EPLAN ERP/PDM Integration Suite.
Digital Twin: an eye on the future
Knowing beforehand how the system will work afterwards – this can be realised with EPLAN Harness proD and is the stuff of which engineer’s dreams are made: “It’s impressive to see how close the actual system comes to the previously designed digital twin,” Bern says, referring to the advantages of the virtual simulation of the battery system on his desktop. “We can check everything in advance with Harness and detect errors early in the process without first having to build prototypes: ease of installation, wire routing with respect to the space in the target application or the accessibility of plug-in connectors. Ninety per cent of the task can be taken care of in 3D, thereby reducing the efforts needed for prototypes to a minimum.”
With EPLAN Harness proD, wire pathways can be defined without a prototype and bills of materials automatically created – this promotes the workflow just as much as the interlinked modification processes. As Bern explains, “Take the example of wanting to change a single pin on a control device: we don’t have to worry at all about whether or not all the drawings and all the derivations have incorporated this change. The tool automatically takes notice, pointing out the change and implementing it everywhere.”
The measurement of wire lengths is also completely automated in EPLAN Harness proD. “That’s a very important point,” Bern says, “even if it’s not the first thing you notice. In conventional wire design, first you construct a sample and then it’s checked for suitability; the wire harness is measured by hand and then the respective drawings and nail boards are designed. All of that happens here with a click of the mouse.”
What’s clear is that there isn’t any application that can’t be used for something exotic. And even Voltabox doesn’t make an exception here when using EPLAN Harness proD: “What we like to do internally is design the tubing in EPLAN Harness. We simply give a wire harness the respective properties for the piping we need to use, and presto!”
Author: Ulrich Kläsener, freelance editor, Bergisch-Gladbach
Voltabox AG
With its safe and economical lithium-ion battery systems, Voltabox AG is considered a pioneer in efficient mobility. Around 275 employees – including 81 in research and development – generated sales of about 67 million euros in 2018. The Group expects sales of between 105 to 115 million euros in 2019 by expanding its business activities in North American and European intralogistics business, not to mention batteries for pedelecs and e-bikes. The market for agricultural and construction machines is also being promoted.
Along with their headquarters in Delbrück, Voltabox also has other facilities in Germany, for example in Aachen, as well as in the US and China. The parent company is paragon GmbH & Co. KGaA.