Full speed ahead in engineering
With EPLAN Engineering Center, Single Temperiertechnik has turned a chronic shortage into a strength that has led to greater competitiveness.
If creating manufacturing documents in the company has become a constant problem, automated engineering can turn a weakness into a strength. Single Temperiertechnik GmbH, the specialist for fluid media temperature control in industrial production and testing processes, has reduced the average time for the creation of circuit diagrams and bills of material for standard products from three hours to between 10 and 15 minutes. This success was achieved with the assistance of the EPLAN Engineering Center. This has resulted in faster turnaround times, improved ability to react to customer requirements and more flexibility in the use of personnel.Single systems are in use in plastics or ceramic processing, die casting or semiconductor technology and in engine or hybrid component testing bays. Single systems are used wherever temperature control and cooling processes take place in the industry. More than 5000 units leave the company's headquarters in Hochdorf (Baden-Württemberg). These range from standard products from one of the various product series up to tailor-made special systems. About a third goes directly into the export trade and there is also a high amount of indirectly exported Single products that are supplied to other system manufacturers. The customers come from the fields of engineering, automotive construction and aeronautics, electronics, pharmaceuticals and chemistry, food and packaging as well as several other branches. Single is an international player and has representative offices in thirty countries.
Employ more staff or automate?
At the beginning of the decade, a point was reached at which the job volume could no longer be managed using the existing methods. The construction department was placed under massive pressure, order backlogs were commonplace and it took too long to determine the materials required. Frank Spork, a member of the management board, had a decision to make. He could either employ more staff that would in turn create more interfaces and thus increase costs, or he could automate engineering.
This decision was made in favour of introducing the EPLAN Engineering Center. This was referred to by the internal designation "configurator" and it was adapted to the specific conditions at Single. This was a logical decision - Single has been counting on EPLAN for decades and is currently using EPLAN Electric P8. Frank Spork explains: "The EEC is perfect for our portfolio, because Single is not just a catalogue supplier; rather we offer our customers individual consultations and configure the standard products to the customer's individual specifications."
The configurator supplies technical documentation that can still be changed. A pilot phase with a simple range of products was carried out initially. Today, 60 percent of Single systems are constructed via the configurator. Of these, around 40 percent require subsequent planning. The configurator is almost always used for this. Only special projects are worked on by hand these days - these are the projects in which the construction process begins from scratch.
A small construction revolution
Changing over to automated engineering was a small construction revolution for Single. Previously, circuit diagrams and bills of material were created separately for each product in EPLAN and in the ERP system. A similar previous product was normally used a template and modified appropriately. The problem with that was that bills of material always had to be individually compared with one another. This meant that changes were time-consuming and there was almost no scalability. On top of that, each product has a variety of parameters – heating or cooling power, temperature spectrum, temperature control medium, pumping output, regulators, data interfaces, as well as input and output signals that also affect the components. Only a handful of experts could cope with all this.
After the changeover to the EPLAN Engineering Center, the expert knowledge is located in the regulatory structures of the configurator and it is constantly being updated. The components are selected via the EEC operating interface of the configurator that controls EPLAN Electric P8 and from which the bills of material are generated. From the startup screen, the series must be selected, and then the standard product that is being used as a basis is selected. The selection fields only provide those components that can be used in the product selected. There is a lower risk of construction errors.
Faster turnaround times, better documentation quality
The circuit diagrams are created using configurator macros and the wiring diagrams are created in EPLAN Electric P8. The bills of material that are generated are transferred into the ERP system, which compares the manufacturing jobs with the stock of materials and places orders where necessary. For small components, an internal Kanban system with series-specific material trolleys has been introduced.
Frank Spork summarises the success as follows: "This has considerably improved the throughput times: An average project can now be created in a quarter of an hour as opposed to three hours - all without any subsequent engineering time. The quality of the documentation is also good as long as the database is kept well maintained." The time saved means that Single can react faster to enquiries and to changes in the course of the project; this results in them increasing their competitiveness. Frank Spork says: "Most of our competitors are producing a range of products that is becoming more and more defined; we want to be faster but we want to still be able to offer a large range of products. Automation in engineering has allowed us to achieve these goals." There is an additional bonus in that order documentation can be produced in German or in English, depending on the project. This is particularly useful if an English documentation for the wide range of export products is required.
Consulting is indispensable
However, the introduction of the EEC configurator required an additional expenditure: The product range needed to be revised and services and options had to be defined. Additionally, dependencies needed to be examined and the modular system had to be programmed. Frank Spork recounts: "Members of EPLAN staff were with us in-house for two years. Creating a new development environment is a complex task, we needed external knowledge and we did not have such capacities within our company. Our staff could not have taken care of this in additional to their regular work." The configurator is now being maintained and developed further internally; for new functionalities, there is often the question of whether they should be programmed in the modular system or whether they should be designed as needed.
It was important for Single to involve the staff from the start. Nobody in the regular team needed to fear "becoming redundant": Frank Spork says: "We can now process more orders with the same personnel, our electrical designers are free to concentrate on developing new technologies and can work as sales contact staff, providing advice to customers." And what’s more: "Standard orders and products that do not require subsequent engineering can be generated by members of staff who are not electrical designers. This gives us more flexibility when planning cover for holidays and sickness."
Costly expenditure, but it pays in the long run
Frank Spork is already forging new plans. EPLAN Fluid has already been integrated into the creation of process measuring and control technology schemes. He can also envisage making the configurator accessible from around the world on a web platform so that the sales team can make their methods of making offers more dynamic and so that the technical feasibility of customer desires can be immediately assessed. Single isn't even close to having exhausted the potential of EPLAN Engineering Center. More information: <link http: www.single-temp.de _blank>www.single-temp.de.
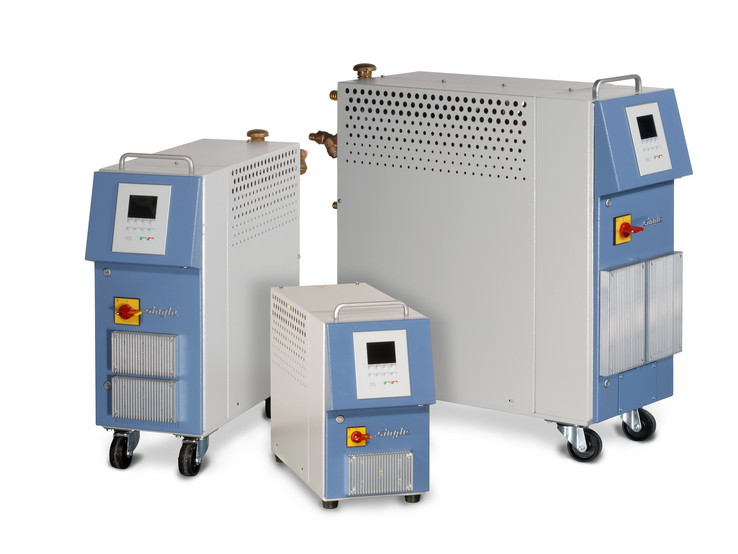
A wide range of products, lots of variants - automated engineering allows us to maintain this competitive advantage.
Image: Single Temperiertechnik
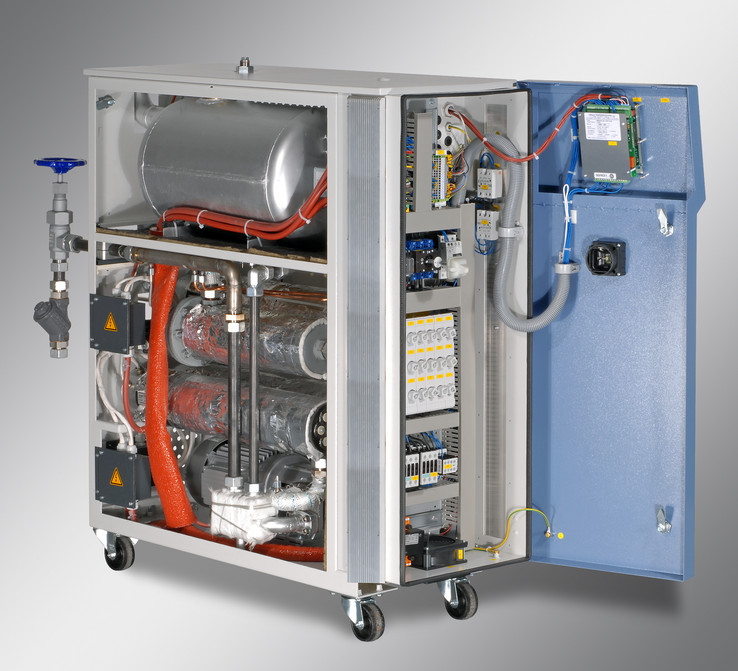
The selection of the components is determined by a variety of parameters - the rules are stored in the EEC configurator.
Image: Single Temperiertechnik
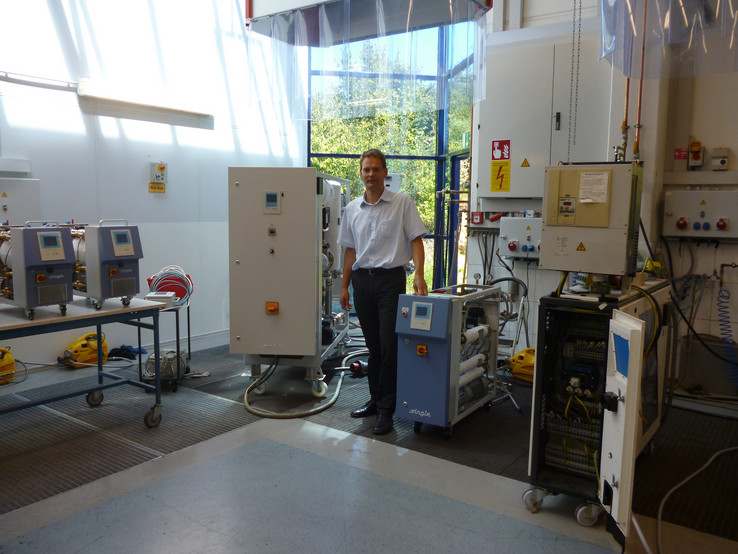
Frank Spork in the Single testing room: "The EPLAN Engineering Center has improved the quality of the product documentation considerably."