Unlimited Teambuilding
Along with the SAP software as the leading system the software EPLAN Electric P8, among other applications, is used to represent electrical and fluid power engineering in one system.
The metal forming experts at the Schuler Group are able to work together in project teams across industry standards. After the takeover of Müller Weingarten by Schuler both IT systems were reconfigured and standardized. Along with the SAP software as the leading system the software EPLAN Electric P8, among other applications, is used to represent electrical and fluid power engineering in one system. This certainly makes collaboration across disciplines much easier, even though a comprehensive mechatronic model is still a dream of the future. "We are able to work together" reports Christoph Kämmerle, who is in charge of system support for the Schuler Group's technical software. "For instance we can have two design engineers at headquarters in Göppingen work with two additional engineers in Weingarten and three other colleagues at other locations – and it can easily set up without problems." The fact that Schuler, with expertise in the metal forming industry, and who has locations in 40 countries, can use such synergies is solely based on a decision made by their management at some point. For instance, in 2007, after the take-over of the Müller Weingarten AG by the Schuler AG, one of the decisions made was to combine the companies' IT systems onto a common base. It was not an easy task, as the IT landscape had developed – like the company structure – over time at Schuler as well as at Müller Weingarten literally over decades. But they were able to reach their goal: Kämmerle emphasizes: "We are now able to balance out capacities between individual company sectors – across locations and technology fields". During mergers of this kind it is important to get a clear view of the basic work processes and to include affected personnel. Schuler applied the Best-Practice approach. Christoph Kämmerle remembers: "Our fist step was to filter out the processes that were working well in the individual companies and to present these to all participants". The processes that fulfilled all requirements best were then adapted so that everyone could identify with them. "We didn't 'force' anything, but worked to find the greatest possible denominator – which really promoted acceptance among the employees." The required effort to achieve this was tremendous, but it was literally a must if one wanted to succeed. "It starts with the smallest details: If the various forms or terminal diagrams cannot be interpreted clearly, the problems can grow far into the manufacturing network." Choosing an IT solution was a similar process. The interesting fact was that Schuler as a technology driven enterprise didn't use a CAD-related PDM system as their primary business application, but an enterprise wide ERP system by SAP. "That was also a fundamental decision: The IT expert states: "We planned to bring together and keep all data in SAP". Schuler works with an add-on software to meet the requirements of the design engineers, among others with the Engineering Control Center ECTR by DSC Software. "This tool provides the required transparency by creating a technical view into the business management software." It provides the designers with the important views, similar to a PDM system, and supports them in routine tasks – which in turn creates space for more creative and innovative activities. "Our use of the SAP-ERP system, the ECTR and our own customizations to accommodate our processes, has made us very productive and able to automate many tasks, all the way to work preparations." Our goal is the inter-disciplinary engineering process
During the course of its IT landscape consolidation Schuler addressed the topic of inter-disciplinary engineering, especially as it relates to the interaction of electrical and fluid power engineering. The problem is: both companies, as they were acting separately in the market before, were successful with a sequential operating principle, where mechanics, electrical engineering and fluid power engineering would follow each other and were viewed separately. Christoph Kämmerle explains: "That only worked, because inside Schuler or Müller Weingarten the paths were relatively short; the developers knew each other and were able to resolve any questions directly with their colleagues. "Each additional location made these coordination efforts more difficult." Schuler as well as Müller Weingarten used the CAD/CAM/CAE solution Catia (Dassault Systèmes) as their mechanical engineering tool, with the related PDM system Enovia taking care of the drawings management task. Even though the project management is steered by SAP, Enovia delivers the required data in neutral formats. The situation regarding electrical engineering was more problematic. In 2007 Schuler was still working with EPLAN 5.70 by the same provider; Müller Weingarten worked with the CIM Team software Promis. However both companies were already in the process of shopping for a replacement for their drawing related programs. The two preferred systems under consideration were EPLAN Electric P8 and E3.Series by Zuken – both are solutions that cover electrical as well as fluid engineering. System specialist Kämmerle remembers: "Both systems, when benchmarked, and proved to be equally suited". "But since our goal was a uniform system environment, we decided on EPLAN Electric P8 – and the consolidation of electrical and fluid power engineering into that software." Today EPLAN's software is firmly established in all business sectors of the Schuler Group. Kämmerle continues: "Now we can – depending on capacities – have the flexibility to have hydraulics developed in Göppingen and the wiring in Weingarten or vise versa. "Beforehand, I didn't think this would be possible, especially the system change at Müller Weingarten." A thorough preparation was the determining factor here as well: The planning phase began after initiation in March 2008, when the connection to the SAP solution had to be thought through, among all the other factors. Because of the global financial crisis in 2008, the first installation was postponed until the end of 2009. Central data storage in the SAP system
Examining the course of an order process may be helpful in understanding how the collaboration among locations actually works. It doesn't matter if the customer orders a standard eccentric press or a customized large capacity plant; either way, the sales department will start by setting up the basic structure in SAP. This is only a rough framework at the beginning, the actual technical specifications will be developed with the experts in the individual disciplines. They will in turn begin their development, with mechanical engineering at the beginning. Electrical engineering then receives an order from the ERP software and builds on the draft of the mechanical design. They work in EPLAN Electric P8 again with parts and material master data information from SAP and thus, create the corresponding components and functions. All required documentation, including power circuit and terminal diagrams, will be transferred from the EPLAN software to the SAP system in the form of PDF documents, along with bills of materials. Christoph Kämmerle explains: "This is where we assemble all necessary documentation as well". "This way we are flexible in the manufacturing network as well, and are able to use unused capacities where they are available." The SAP solution is technically able to provide the correct records as needed. Last, but not least, this also includes all aspects of company know-how protection. "We can then contract out hydraulic aggregates or enclosures to suppliers – but our core know-how will stay in-house!" Schuler relied on the ETIM standard (www.etim.de) for standard production of repeat parts. Kämmerle reports: "We adopted its structure to about 80 percent, the other 20 percent were customized for our company specifically". The flow goes as follows: all data is first prepared in SAP and then synchronized in the EPLAN software. The designers are then able to look for (and find!) their components in EPLAN Electric P8. "EPLAN is clearly the leading system for this task." Excel sheets are a thing of the past – considering the approximate 530,000 purchased and standard parts in a large-scale system – this is not surprising. One system for electrical and fluid power engineering
EPLAN Electric P8 and its EPLAN Fluid add-on allow Schuler to service electrical as well as fluid power engineering – climate control and lubrication are also included, alongside hydraulics. Christoph Kämmerle emphasizes: "For example, we are to the point where an electrical or fluid power component is assigned only one device designation – before this it could have been up to three, depending on the disciplines involved." Mechanics was interested in the element to be switched, the electrician the switching state and the hydraulics department the final controlling element. "That is no longer the case; we only have one component, which is only listed once in the device list." Furthermore, it has been assured that the correct component can be located, thanks to the preparatory classification work in SAP. The merger of electrical and fluid power engineering has not advanced deep enough to satisfy Schuler employees. "A remaining problem are the world of standards, which have not converted to the mechatronic processes and are still not viewing things as a single unit." So far there is no one all encompassing standard; each trade still has its own directives. "A software tool is not able to compensate for that, so we still need to find our own solutions – that was one of the most difficult hurdles to overcome during the implementation process." Christoph Kämmerle recognizes a shortcoming in one other issue. "So far we have not been very successful in running all relevant design data through all the systems continuously – like a complete system description or the time factor alone." This holds true for Catia as well as EPLAN and is supposedly a problem for programming machine controls. "So far the process runs as follows: The sales department sells a function, the corresponding mechanics are modeled, the fluid power technician adds the valves, which are then switched by the electrician. But now the programmer needs to know when, or at what point, the mechanism will be activated – this information is missing in the past design processes!" There is still much to be done in this area in order to store such information continuously and across disciplines – based on the specifications of the respective experts in the technology. "When we are successful in reaching this, I am able to look at further aspects and analyze a design more in-depth." For example lets look at the question of how quickly the machine can be shut down, or what costs are related to which component. "In this case the issue of transfer and finally the protection of company know-how has not been resolved to our satisfaction." Service has access to current configurations
All server hardware for the ERP and M-CAD, as well as the E-CAD software, have been concentrated at the headquarters in Göppingen. Employees access them via terminal servers and are therefore always able to work with up-to-date data. The service department is able to access all relevant data of any particular plant via the SAP system – even mobile and on-site via a VPN connection. If necessary, the design department is involved to resolve errors. This facilitates timely reaction and makes sure that all safety mandates have been complied with. There is one disadvantage though; if modifications are performed after the fact,including remodels of existing plants, old Promis data cannot be read into the EPLAN Electric P8 system. The only solution provided by the Müller-Weingarten part of Schuler is to import DXF data and revise it as needed. Importing legacy data is not without risk, depending on the age and functional degree of the systems. The next step is to focus on the topic of customer documentation and its standardization. "By far the greatest need is in E-CAD – where several thousand pieces of paper will have to be processed", explains Kämmerle. "This can be done with the EPLAN software, but a structured approach is required to be able to tie in the information from the other disciplines." An interesting point: Schuler no longer compiles a bill of materials of device list from the individual systems for the customer. "All data is fed into the SAP system, and then we need to revise it a second time for compiling our customer documentation – we can therefore combine this task and complete it more efficiently." Published in CAD CAM Report, Hoppenstedt Verlag, Edition 11/11

Schuler's program includes standard presses (small picture) as well as large-scale mega plants for sheet metal forming, which can contain up to 65,000 designs, as well as 530,000 purchased and standard parts.
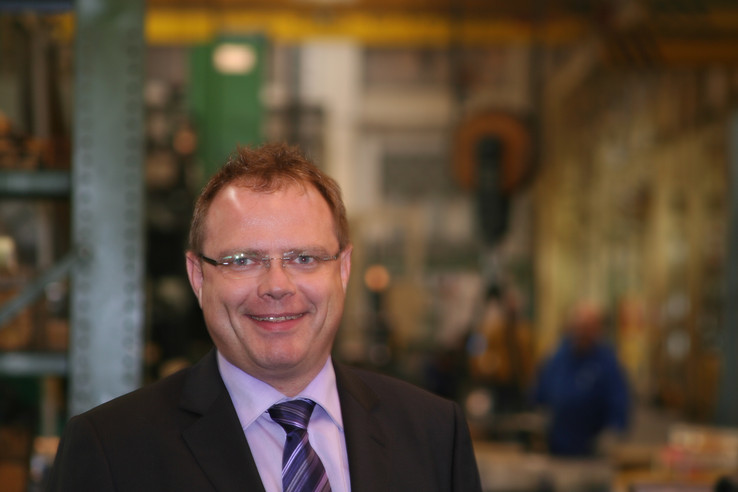
"Because of the uniform, enterprise wide IT architecture, we can facilitate a capacity exchange between individual sections of the company – across locations and technical specialty fields". Statement by C. Kämmerle, in charge of E-CAD system support.
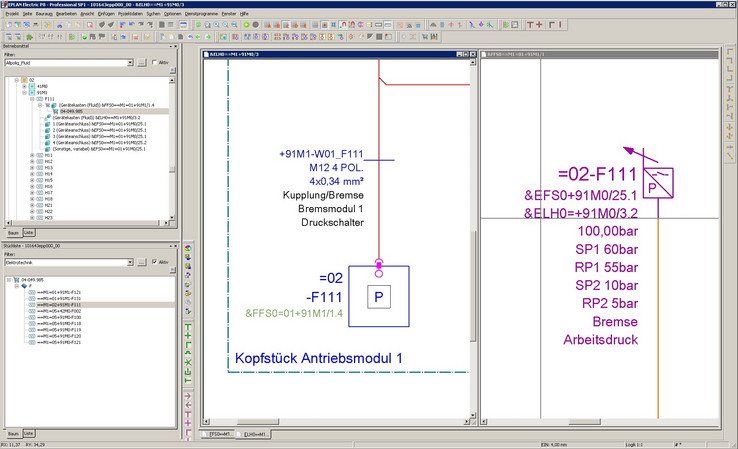
EPLAN Electric P8 is the tool for electrical and fluid power engineering for everything except mechanical engineering.