Schaeffler: Rational electrical engineering in "batch size of one"
The Schaeffler Group sees itself as a leading innovator in this demanding area of drive technology, and has a separate department for test bench construction at its headquarters in Schweinfurt.
It is known as Astraios, weighs 350 tons and can apply a total force of 10 Meganewtons – corresponding to a load of 1000 tons. We are talking about the new test bench that Schaeffler recently started up at its Schweinfurt location. The equipment is used to test large roller bearings, which are mainly used in wind power systems. The demanding project was completed by the company's in-house test system construction and special machinery construction departments within a short planning and construction time. The entire electronics of the test bench were planned using EPLAN Electric P8. Large roller bearings, which are mainly used in wind power systems in the multi-megawatt class, have a service life of at least twenty years under extremely dynamic loads. The developers often come up against the boundaries as far as material, drive and construction engineering are concerned, which makes comprehensive test bench trials all the more important. The Schaeffler Group sees itself as a leading innovator in this demanding area of drive technology, and has a separate department for test bench construction at its headquarters in Schweinfurt. The electrical planners in this department have been working with EPLAN CAD software for about 25 years. Some of the projects are customised systems, which are manufactured in batch sizes of 1. However, the electrical constructors have created a comprehensive library of macros in the EPLAN software, which can be used as system modules on new projects and therefore reduce construction time considerably. The macros model all repeatedly occurring electrical components and functions. They have deliberately been finely granulated so that as many components from the library as possible can be used, even for unusual requirements. In this way, the electrical constructors can also work through large projects in a rational way and plan all switchgear in accordance with identical principles. High complexity of drive and measuring technology
A large project like this came up at the end of 2009, when Schaeffler started to plan a new test stand for large roller bearings at the Schweinfurt site. The demands were considerable: It was going to be the biggest test bench of its kind in the world, subjecting bearings with an outer diameter of up to 3.5 metres to the typical loads that occur. Large bearings like this are currently used in wind power systems with output of up to 6 MW.
The electrical designers were faced with the challenge that the controller had to simulate extremely complex overlaid movements at the drive side. Around 450 digital inputs and 260 outputs were needed. There were also the lubricating units for the test subject, with 12 metering units that can be controlled exactly. At the measurement technology level there were about 350 sensors and an appropriate number of analogue inputs and evaluation facilities. In spite of a considerable amount of experience in constructing test systems, the 20-man team under project leader Reinhold Korn was therefore entering uncharted territory in many respects. The estimated planning and construction period was just two years – comparatively little for such a complex and special system, which weighs around 350 tons and requires an electrical connected load of 2200 A. New platform speeds up construction
For this reason, Leonhard Keller and Heiko Gründl, who were responsible for the electrical design, both worked on the mechanical design at the same time. And they had to overcome another challenge: the large test stand was the first project that they had dealt with using EPLAN Electric P8. Since this is a completely new system platform compared to the previous EPLAN 5.70 system, the procedure was not exactly textbook – normally you would choose a smaller project to start with and not the company's most ambitious project to date. However, the fact that they were able to migrate the existing macros from EPLAN 5.70 to the new EPLAN Platform helped the planners. And they benefited from the fact that EPLAN Electric P8, the CAE system of the new platform, speeded up many individual processes during the planning process, therefore making it possible to work in a much more rational way. A demanding project
Keller and Gründl planned an electrical system that consisted of the individual hydraulic cabinet, lubricating oil cabinet, drive cabinet and measuring rack functions and had a total of 9 metres of switch cabinet (plus a 1.6 metre reserve). They implemented some interesting technical innovations when doing this. The three hydraulic pumps which move the cylinders, each with output of 160 kW, are switched on in a cascade-like way without interruption, in accordance with requirements. Schaeffler programmed the controller for this energy-saving operating method himself. SARA (Schaeffler Automation System for Research & Development Applications) is responsible for controlling the entire measuring technology process, from drive actuation to data measurement, recording and visualisation It generates the wind load setpoints, controls the servo cylinders and collects the measuring data. The measurements on the moved test subject also make special demands with regard to measurement transmission. A great deal of information is transmitted wirelessly. Production equipment is also used
Two items of production equipment were integrated in the test bench: a measuring system for monitoring vibration, which provides information about the condition of the roller bearing, and a particle counting system, which monitors contamination in the bearing's lubricating oil. The electrical planning for these two systems was simple – the sets of drawings, just like the devices themselves, were fully integrated in the project. The first tests on the new test bench (Picture 4) revealed that the measuring results and the calculations corresponded. The "Test" department now uses the test bench intensively in order to look for optimisation potential for developing new roller bearing generations which also improve their calculating principles. In the near future: Fluid engineering integration
For the near future the persons responsible for the electrical and systems engineering in test system construction are planning to extend the EPLAN Platform by adding the EPLAN Fluid (for fluid engineering design) and EPLAN Pro Panel (for switchgear construction) modules. The responsibility for planning the fluid engineering is therefore being transferred from the mechanical construction area to the electrical construction area. The procedures in test system construction speak in favour of this modified form of work distribution – the electrical planners do not need to manually re-draw the plans that they receive from colleagues, but can continue to work on the existing platform. Astraios: A giant for measuring and testing technology
The large roller bearings that Schaeffler manufactures for wind power systems in the multi-megawatt class have an outer diameter of up to 3.50 metres and weigh up to 15 tons. These bearings are subjected to extremely high loads. The hub with the rotor blades, which weighs up to 100 tons, introduces radial loads into the bearing; the highly dynamic wind force mainly generates axial loads and torques The developers were previously dependent upon calculations during the construction of large bearings for multi-megawatt systems, which withstand these high loads over the required service life of 20 years. Schaeffler can now fall back on real data. This is because the new large test bench "Astraios", which is named after the father of the four wind Gods in Greek mythology, realistically simulates the practical conditions to which the roller bearings are subjected. This is taken care of by four hydraulic radial cylinders and four axial cylinders, which individually generate force of 1 or 1.5 Meganewtons (corresponding to 100 or 150 tons). The movements can be overlaid and varied in an extremely dynamic way – just like the way the wind blows at the rotors high above. During the bearing movement, about 350 sensors record values such as temperature, pressure, torque and expansion, which are displayed, documented and evaluated. Schaeffler has invested about 7 million Euros in this system, which can test roller bearings for wind power systems with output of up to 6 MW. This does not just make Astraios the most modern large bearing test bench in the world, but also the biggest and most powerful.
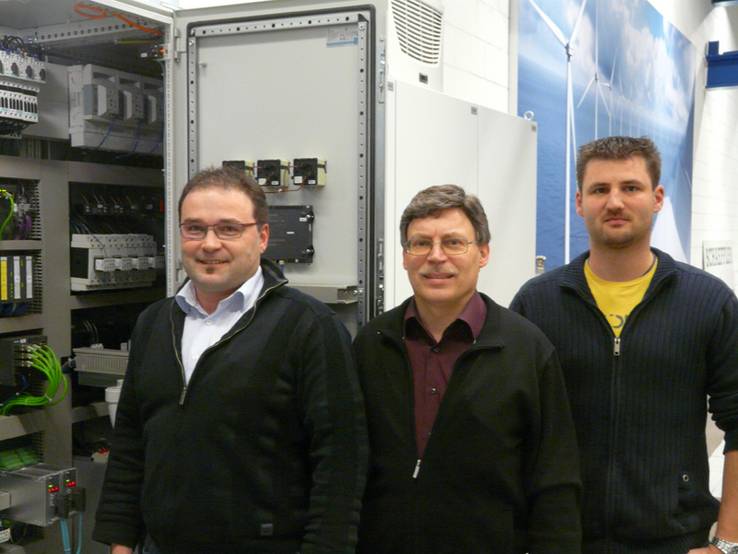
The electrical planners of the Schaeffler test system construction area Leonhard Keller (left) and Heiko Gründl (right) with project leader Reinhold Korn (centre) in front of one of the test bench switch cabinets.
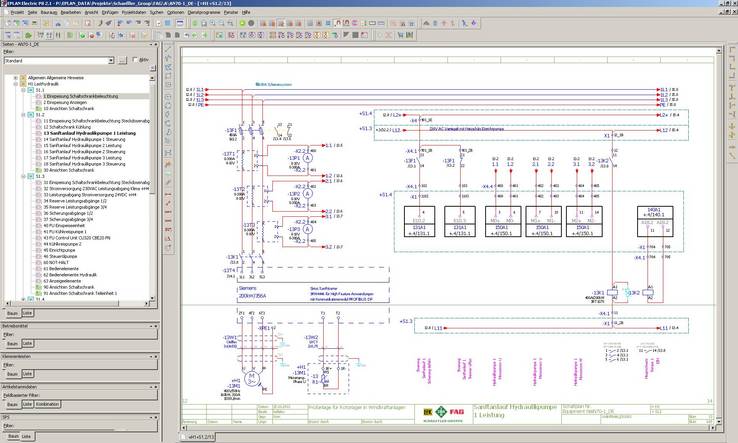
From floor plan to detail: The entire electrical planning of the "Astraios" test bench was carried out using EPLAN Electric P8.