The Code to Greater Efficiency
Protec designs, builds and programs customised instrumentation and control technology for buildings and plant systems
To realise consistent and reliable building automation, Protec Technologies has implemented a comprehensive solution encompassing all the trades. The company designs, builds and programs customised instrumentation and control technology for buildings and plant systems, and – with the help of EPLAN – was able to make its processes more secure and considerably more efficient.
In Germany, buildings account for about 35 per cent of consumer energy consumption and about 30 per cent of carbon-dioxide emissions – more than vehicle traffic or industrial uses. Reducing these energy demands is therefore a focus of climate protection legislation: legal and regulatory requirements have been increasing for years. Yet that’s not the only reason that building automation is booming; standards for health and comfort, not to mention safety and security, are also higher today than they were a few years ago. Building automation is thus playing an increasingly important role in automatically carrying out processes according to predefined settings or simplifying their operation. Sensors, actuators, control elements and other technical units in the buildings are being networked with users.
Protec Technologies was founded by Rolf Martens in 2004 as a one-man company. Today Martens employs 24 people for the planning, design and implementation of I&C technology in buildings and process automation. Last year Protec moved into a new, larger building that offers room for expansion. CEO Martens: “Based on customer-specific planning, we offer everything from building visualisations, design, construction and programming to plant system equipment, switchgear system engineering, VPN plant networking and assembly. These all include service, maintenance and remote maintenance, of course.”
EPLAN software solutions and services have been used practically since the company was founded. “EPLAN supports us throughout the entire process, from preparing quotes through to service and maintenance,” says Protec Technologies Design Manager Armin Schwarze. EPLAN Electric P8 is used for generating schematics and bills of materials, device management and generating labels, while EPLAN Pro Panel manages such tasks as mounting plate assembly, wire routing and 3D control cabinet designs. More recently, EPLAN Preplanning has been used to create control diagrams, preplan system overviews and design the building automation. The terminal strip setup and configuration are carried out in Clip-Project by Phoenix Contact.

Protec Technologies employs 24 people at its recently relocated headquarters in Neudrossenfeld, Bavaria. Two additional employees work from a field office in Thuringia.
Picture: Protec Technologies
From Preparing a Quote to Maintenance
Martens: “We initially tested a commonly used solution for building automation – actually a good tool, but it had a distinct disadvantage in that data continuity couldn’t be guaranteed. That’s why we decided for EPLAN as an integrated solution. And we’re still very happy about this choice today.”
The most recent project with EPLAN was last year with the introduction of EPLAN Preplanning. “The software offers the possibility of reproducing the structure of the customer’s site, the entire factory, its buildings, its property and its plant systems,” Schwarze explains. One goal with this was to shorten the design phase. “And we’ve already managed it,” Schwarze adds. EPLAN Preplanning offers a structured acquisition of the process and instrumentation data and its management. Schwarze and his team can use it to quickly generate initial data sheets and specifications. Among other things, this allows a structured layout to be created for materials procurement already in the preplanning phase.
Another major reason for introducing EPLAN Preplanning was the increasingly frequent requests from Protec’s customers for the creation of what is known as a plant identification code, or PI code, a uniform identification system for technical building equipment. Each separate element within the code contains information, including the building designation, the information focus, trade designation (e.g., electrical), type of system and functions such as temperature or humidity values. Plant systems and components can be uniformly and consistently designated and described in this manner. Schwarze: “Preplanning automatically generates the PI codes that we then use to generate schematics, for example.” Previously the PI codes were generated via data that was manually entered into Excel lists and had to be added to an Access database. “You had to be careful not to create any duplicates,” Schwarze says. “It was a very complex and error-prone process. EPLAN now does it automatically at the push of a button. All in all, project runtimes can now be reduced by up to 20 per cent, as our initial experiences have shown.”
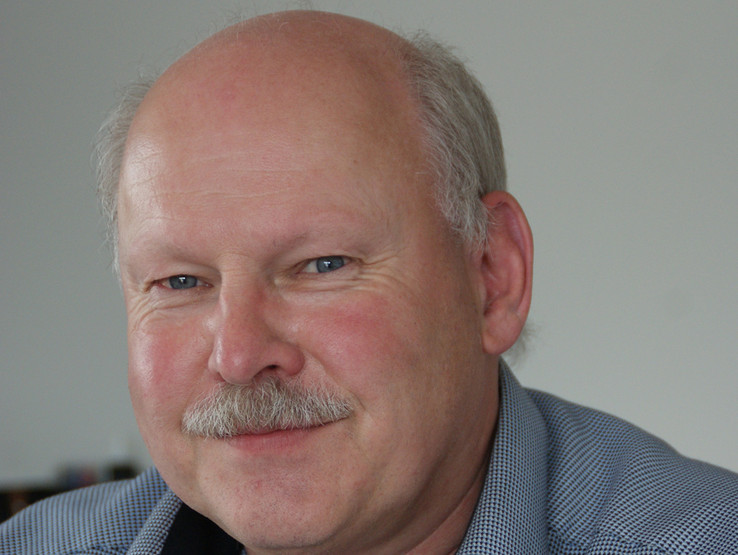
CEO and Protec Technologies founder Rolf Martens: “If we use the EPLAN solutions consistently and correctly, then the possibilities are fantastic. We can also generate new business areas and make ourselves more competitive.”
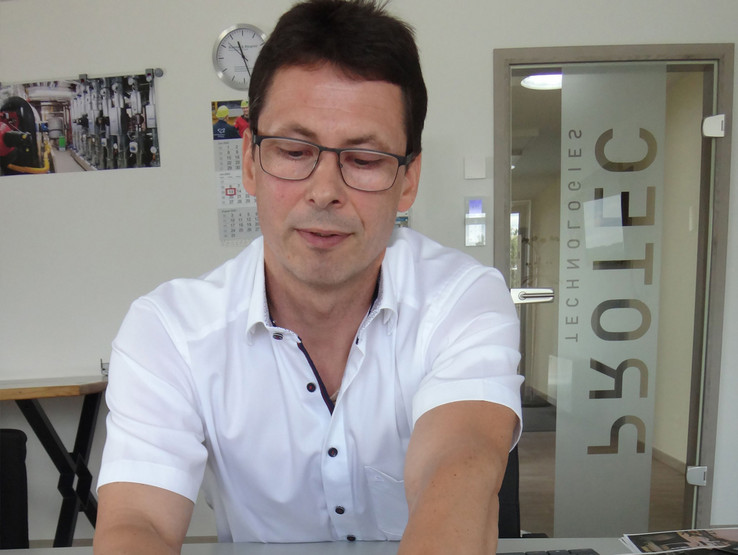
Armin Schwarze: “Using the QR code that we generate in EPLAN Preplanning and place on every component, the customer or our technician can always access all the information about it through the cloud.”
PI Codes Increasingly in Demand
He demonstrates how simple his work has become with the example of the planning of the I&C technology for a hospital in northern Bavaria, a strongly competitive tender for bids that Protec won. “We were able to put together an attractive offer,” Martens says, “and naturally the work and time saved by using the EPLAN solutions played a role. The project is worth 1.15 million euros and will take two years. It’s a great success for us.” Protec Technologies is working on this project together with an engineering office, which provides the operational data for the plant systems. Schwarze: “We receive data lists in external formats that are not in a form that we can work with.” However, EPLAN can use and process the data, which arrives either as CAD data based on DXF or as simple PDF files.
“When we have the control diagrams as DXF or PDF files, we import them into Preplanning and supplement the data with intelligent information. But if I have to draw up a comprehensive P&I, for instance the heating control diagrams, then I need a whole day,” Schwarze explains. “This way we can feasibly store only the image and specify the PCT locations. EPLAN Preplanning simplifies the work process here. Instead of spending an entire day drawing diagrams, we now need only a fraction of the time depending on the number of data points.” Schwarze then defines all the important data that are needed in the diagram so that the software can create the PI code. “This is created automatically, throughout the entire structure, the entire factory, the entire system. What’s great about it is that if there’s a change, for instance a different component or a type change, all the corresponding data is changed throughout the entire structure. It was quite a lot of work in the past to change all the schematics, Excel lists and so forth.”
Customers also need the PI code more and more frequently. For instance, it can be imported into the Siemens Desigo CC platform and used there for building management. “The PI code is increasingly becoming part of the specification,” Martens explains. “In the hospital project, we will probably end up with up to 2,500 data points.” Although Protec has also handled projects with even more data points. Rolf Martens: “Today, the PI code plays a major role for around 60 per cent of customers right from the start. EPLAN Preplanning offers us the possibility of a detailed cost calculation for the customer and lines of reasoning for explaining cost changes.”
Although prices aren’t included in EPLAN Data Portal, it does have all the other technical data of the components for plant system designs. In the cloud, Schwarze can select the correct components from over one million data sets from hundreds of manufacturers and put them in his project. The data of the individual field devices, such as room sensors, can then also be called up in Preplanning. Schwarze can see which measured values need to be used for the specific plant system or which control signal is processed via the individual dashboards. “Even the programmer can already read off from the information how the programming, scaling and so on must be aligned. Otherwise it was always necessary to look it up beforehand, which required considerable additional effort,” Schwarze says. Often something changes while the system is being designed, for example a room sensor becomes a humidity sensor. Schwarze: “A mouse click changes the measuring ranges and the original schematics at the same time. It’s a huge relief.”
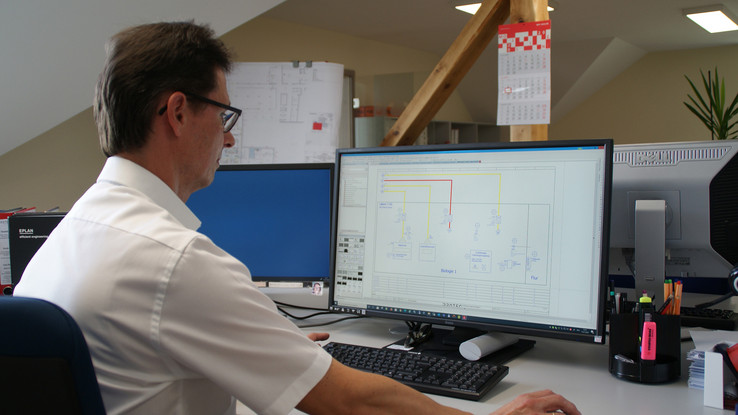
Design Manager Armin Schwarze is the EPLAN specialist at Protec Technologies: “Thanks to EPLAN’s great training and the easy user interface of the solutions, creating additional programs or macros isn’t a problem at all.”
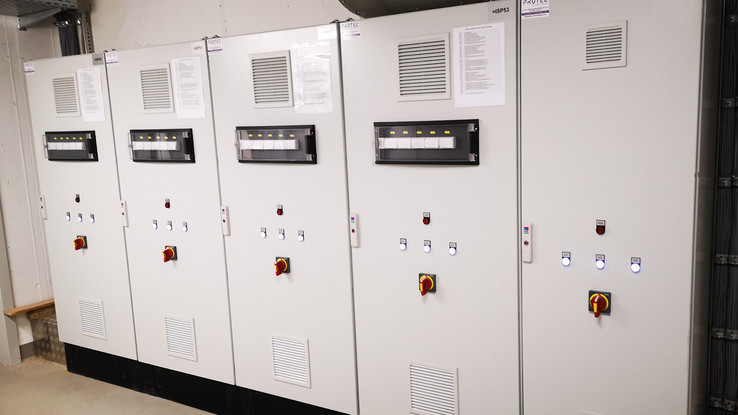
Protec Technologies works with two suppliers to build control cabinets. They receive all the necessary data, including the schematics and bills of materials, directly from EPLAN Electric P8.
Photo: Protec Technologies
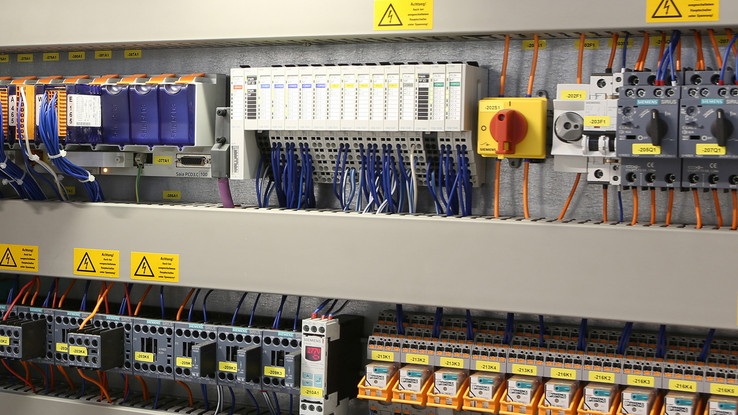
If the schematics aren’t inside the control cabinet for some reason – the customer always receives a paper copy – the customer can scan the QR code and download the schematics online. Then they have all the available information.
Photo: Protec Technologies
Creating Labels with QR Codes
A further simplification is the possibility offered by EPLAN to provide each system field device with a label containing a QR code, a feature Protec Technologies also uses. Firstly, the customer can be offered maintenance recommendations in plain text on the label, and secondly, the QR code can further be used to provide the customer data sheets that are stored in Protec’s in-house cloud, for example.
This gives customers online access to all their inventory documents and schematics. As Schwarze explains: “If the schematics aren’t inside the control cabinet for some reason – the customer always receives a paper copy – the customer can scan the QR code and download the schematics online. Then they have all the available information.” Martens adds: “If one of our technicians is on site for maintenance and discovers that something is wrong with a room sensor, they can record this, immediately upload it to the cloud and then place the sensor on the order list as a spare part.” This considerably simplifies maintenance. In addition, the company is already thinking about setting up an app service based on the QR code. Aside from providing customers a better overview of the field devices used during preliminary planning, this also makes it easier for them to order spare parts after the plant has been built. “If we use this consistently and correctly, for instance with the QR code from documentation to service, then the possibilities are fantastic. We can also generate new business areas and make ourselves more competitive,” Martens says. Initial app testing is already underway at Protec.
Martens and Schwarze are also already thinking about the next steps of their integrated EPLAN strategy: connecting their ERP solution to EPLAN’s ERP/PDM Integration Suite in order to directly exchange company data such as costs, prices and so on. Martens: “This would make order and follow-up management, cost-centre calculation and post-order calculation much easier for us.”