Fully exploiting the potential of automation
Integrated control cabinet design and production at Ingela GmbH
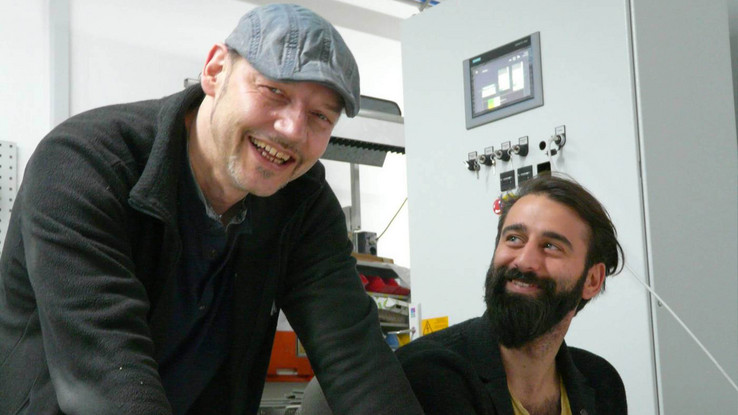
Ingo Straub, Managing Partner of Ingela GmbH (left), with Michael Rauscher, Head of Software Development.
©Ingela GmbH
Over the past five years, Ingela GmbH in Bisingen has grown rapidly from a pure control cabinet manufacturer to a provider of mechanical engineering services. Key prerequisites for this have been a step-by-step development and expansion of the EPLAN Platform as well as direct linking of EPLAN solutions, e.g. to wire assembly and mechanical processing.
Since its acquisition by Ingo Straub in 2013, Ingela GmbH in Bisingen has gone from being a contract manufacturer for control cabinets to a qualified service provider in electrical design.
Investing in automation from the outset
The company was founded in 1982, and when taking it over, Straub – who had previously worked as a project manager at Ingela – instantly made a direct strategic investment in modern software. "We had automated individual areas of control cabinet production, in particular wire printing, as early as 1999, but the existing ECAD system was not capable of undergoing further automation steps. We had to perform many tasks manually or manually transfer data from one system to another".
Step one: Designing with EPLAN
To be better prepared for the future and to develop the company into an engineering service provider, Ingela set up the first EPLAN workstation in 2013. According to Ingo Straub, the company is therefore following a clear principle: "We want to fully exploit the potential of automation".
Step two: Routing with EPLAN Pro Panel
This laid the foundation for further automation. In a second step, Ingela introduced EPLAN Pro Panel for 3D cabinet assembly and especially for routing. The company is regarded in the industry as a specialist for wire processing and printing, so this move extended one of its core competences. The benefits of EPLAN Pro Panel became obvious very quickly: "Error rates went immediately to zero, every length of wire length fits perfectly, and the control cabinet also looks much better". A semi-automatic machine performs wire assembly.
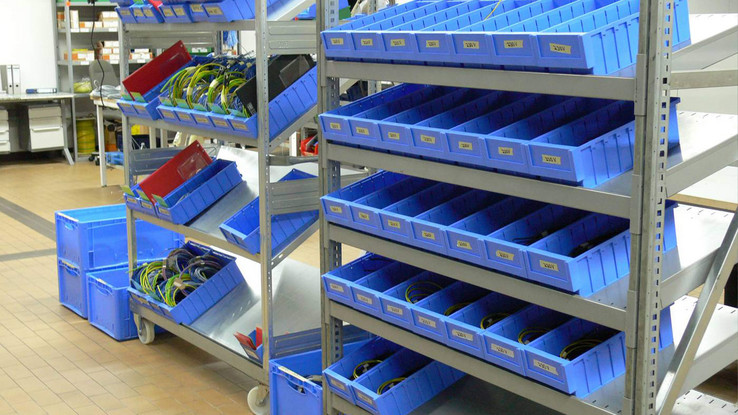
At Ingela, wire assembly is optimally organised and always performed in-house.
©Ingela GmbH
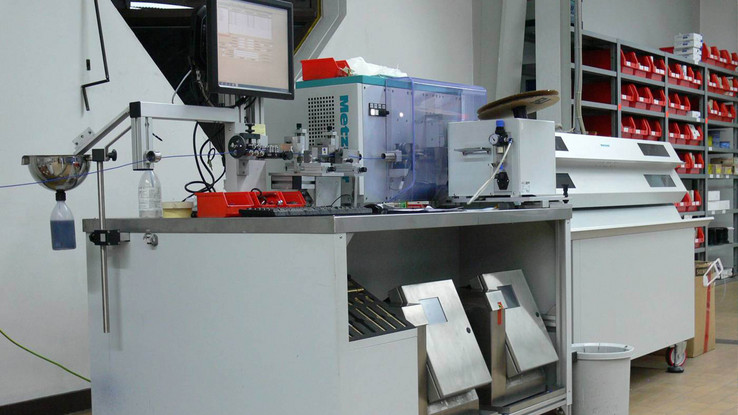
Relatively new is the automated mechanical processing. Directly linked to EPLAN, of course.
©Ingela GmbH
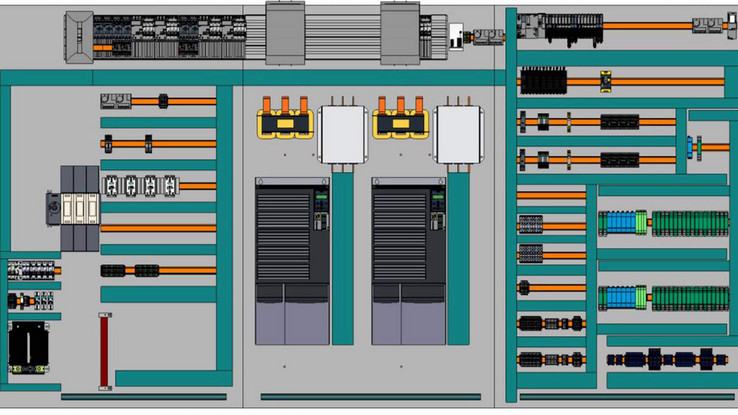
Layout of a mounting panel in EPLAN Pro Panel
©Ingela GmbH
Step three: Linking to mechanical tasks
In 2015, a Perforex machine was purchased for the mechanical aspects of control cabinet engineering, and linked to EPLAN. According to Ingo Straub, the integration instantly delivered good results and significantly shortened lead times in production. It functions particularly well with the Rittal cabinets, which Ingela uses unless the customer specifies otherwise: "Everything fits". This applies also to calculating the climate conditions in a control cabinet. Power dissipation can be specified for each item listed in EPLAN. This makes it very simple to then determine the optimal size of an air conditioning unit (also from the Rittal range).
Even with more complex projects, mechanical design and production deliver perfect results. "A Swedish customer wanted us to use stainless steel control cabinets made of Swedish steel. The customer supplied STEP files for a three-panel, continuously welded cabinet in which the three-part mounting panel and thus also the busbar system (Ri-Line 1600A) had to be inserted laterally across all three panels. This required high precision interaction between planning and production which worked excellently, as did the automated routing over a width of 3.60 metres. The customer was very pleased. Without 3D planning, it wouldn't have worked so easily and smoothly."
The Ingela team also receives constant praise from visitors for its systematic approach. "When visitors produce a control cabinet themselves, and we explain our processes, they often remark that in comparison to us, they're still working in the stone-age". It is therefore no surprise that Ingela was able to gain new customers, e.g. from micro CNC machining and medical technology.
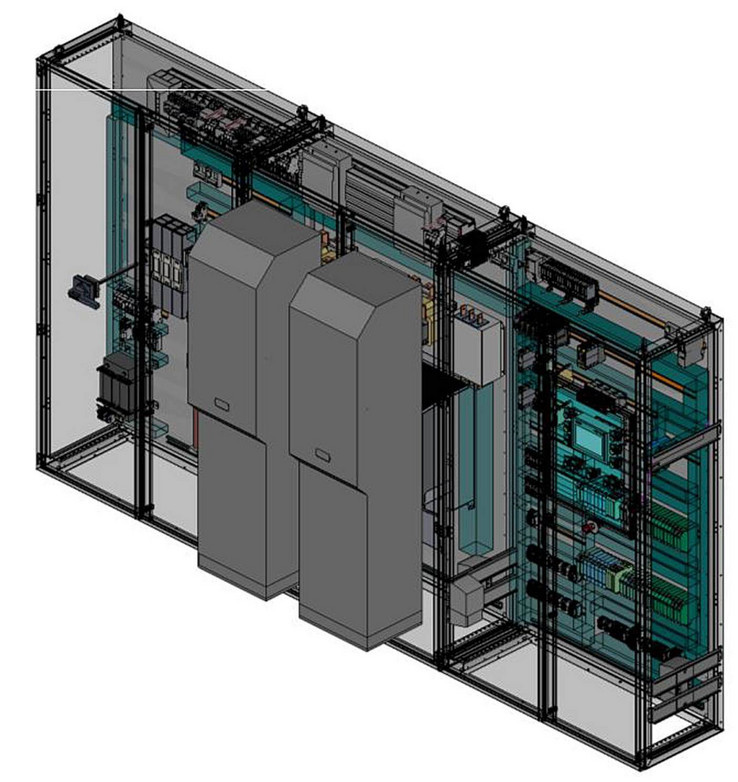
3D view in EPLAN Pro Panel
EPLAN Data Portal supports product searches
Ingela aims to always use the latest components and functions in engineering and frequently accesses the EPLAN Data Portal when selecting parts. Ingo Straub: "The portal has grown considerably over the past three years. It has plenty of data, the manufacturers provide 3D macros, and you can search very specifically for articles and solutions".
Exemplary engineering
The following is an example of Ingela's current approach as an engineering service provider. A manufacturer of machines for wire mesh production had previously purchased its control cabinets in the USA but was now looking for both a European source of supply and a new controller concept. Michael Rauscher, Head of Software Development at Ingela: "The main drives were controlled by four frequency inverters with controllers and a central PLC. This led to vibrations and errors. We proposed servo drives with axis controllers and developed the concept in our company as a trial system. The customer was amazed. The drives can be controlled extremely precisely and there are no more vibrations". It is exactly these kinds of tasks that Ingela has been working towards over the past five years and for which the EPLAN software is being used intensively and systematically. Ingo Straub: "The EPLAN Platform enables us to design for specific requirements, propose solutions and manufacture highly efficiently ".
Division of tasks between mechanical and electrical engineers
The skilled worker shortage is not only a highly topical issue in the Zollen-Alb district and is a reason to mention another advantage of integrated and automated processes. At Ingela, the mechanical aspects of production, e.g. pre-assembly of panels with load-breakers, handles, axles, top-hat rails, wiring ducts, earthing and displays, is performed beforehand by mechanical engineers. Qualified electronics engineers can then concentrate on the electrical part of the control cabinet assembly and wiring. This division of tasks also speeds up processing times.
Summary: Worthwhile investment
The result of Ingela's investment in an integrated, powerful ECAD system with a link to production can easily be expressed in figures. In just five years, the company has grown from 10 to 30 employees and has been able to increase core customers regularly ordering control cabinets from 8 to over 30. Production space also became very cramped. Ingela therefore relocated its production site in the 4th quarter of 2018. The new building covers 2,800m2 offering a production space that is three times larger. The main reason for this growth is the systematic changeover from being just a control cabinet maker to becoming an engineering service provider. Core to achieving this has been the EPLAN Platform.