Configuring instead of designing
The Hörburger AG uses an engineering tool for planning their building automation systems, which allows the automatic generation of project specific technical documents.
The Hörburger AG uses an engineering tool for planning their building automation systems, which allows the automatic generation of project specific technical documents. The basic planning data for heating, ventilation and climate control technology is stored in the system, and the designer can simply plan the plant with the aid of a configurator. This represents a time savings for Hörburger, keeps planning more flexible and increases the quality of the entire process. Hörburger AG, headquartered in Waltenhofen, close to Kempten, has 150 employees and is considered one of the leading system providers for building automation. In 1974, at the beginning, Kurt Hörburger founded the company as an electrical engineering design office. His first portfolio expansion was into the manufacture of electronic enclosures. Hörburger offers its customers a broad engineering and services portfolio, which also includes web-enabled remote monitoring of the installed plants. Complicated projects are daily routine business at Hörburger. The proof is in their service to large banks or retail businesses located throughout Europe. Ever increasing automation energy standards that have to be met in the buildings of today, bring additional complexity to building automation.
An early start in the automation industry
Hörburger had given the automation of complicated building automation serious consideration for years. Detlef Krist, board member Hörburger AG: "For example, we offered a thesis topic that examined the possibilities of automation. But the results were still disappointing, because the CAD tools were not in place for it yet. Until the introduction of EPLAN Electric P8 there were only pure drawing programs, which were not set up for meaningful automation."
A new approach with P8 and EEC
Introducing EPLAN Electric P8 made a new approach, a simplification of processes possible, especially since the "EPLAN Engineering Center" could now be implemented as well. We therefore decided to proceed with both steps at the same time. The EEC facilitates the compilation of a "modular design kit", storing individual component data or modules across disciplines. This means: when a designer chooses a model, the dimensions and connection sizes (M-CAD) as well as the E-CAD data are transferred into the design. The user decides the composition of the module – meaning if it is to be based on small individual components compiled by the EEC or larger assemblies. Hörburger began the Project with careful preparation in 2007 by hiring Andreas Rusch directly after his graduation from a University of Applied Science. Detlef Krist: "We intentionally assigned the task of implementing P8 and EEC to a new employee, as he would be able to use an unbiased approach.
In-house development: "Function oriented configurator"
A modular engineering kit was established piece by piece, completely customized and adapted to the requirements of the Hörburger design team. During that time EPLAN was on-site to support Hörburger with training and consulting. The result of this effort makes the work of the design team associates considerably easier: they use the functions of the respective project as a guide and simply select the appropriate components, like pump, fan, temperature sensor, controller and I/O modules from the configurator. Andreas Rusch: "Macros containing all relevant data have been stored for all projects, and the options that will be queried during the next phase are then stored individually respectively. For instance, when a designer decides on a Type X pump, he will be asked for the type of controls that are possible for this specific pump type."
New processes decrease time by up to 60%
Based on the options selected by the designer in the configurator, not only are the schematics generated automatically, but also the I&C plant schematics for heating and ventilation. The first advantage of this is that plans and lists always have the same appearance. Naming and cable colors will now follow consistent specifications. This will later be a distinct advantage for the installation team on-site. But even more important is the aspect of higher flexibility. Christian Hörburger: "We are able to start planning before all the details have been finalized. This produces a time savings of up to 60% for electrical and I&C design." In addition, the company can change plans and suppliers, upon customer request, or make other modifications without problem: the EEC will automatically generate all changed documents. The data point list, along with the schematics, will be automatically adjusted to the changes.
More than 1000 projects done with EEC
Planning data is transferred per CAM directly to the Perforex machine for sheet metal processing; even cable labeling is done automatically from within EPLAN Electric P8. In this way Hörburger automated an important step from design to production. The designers at Hörburger have processed more than 1,000 projects with EPLAN Electric P8 and EEC since their implementation, all of them with overall positive experiences. Christian Hörburger: "Of course we had some employees that were a little skeptical at first, but now they are all convinced, especially since we adapted our internal organization to the new processes and systems. The engineering tools are constructed simply and have a multitude of applications. The design quality is definitely higher and the error rate lower."
Self-created supplemental functions
Hörburger developed the EEC macros entirely themselves, as well as the basic structure and details of the configurator. Some supplemental functions are part of the individualized special features of the system. Andreas Rusch: "Internal and public notes are recorded for each project. Special notations like memos from customer consultations are a part of that. This also makes it easier for the designers to find their way around a project, for a vacation replacement for instance." The notations can be exported into an excel file and handed to the project manager as a questionnaire.
The next step: 3D enclosure layout with Pro Panel
At this time the enclosure manufacture, which is done centrally in Waltenhofen for all the engineering locations, has not been standardized yet. But this is about to change, when Hörburger migrates from EPLAN Cabinet to the new EPLAN ProPanel Professional. The CAE system will then determine the component placement in the enclosures as well, and the EEC can generate layout plans automatically. Complete automation of the engineering process has been realized with this step. The desired building principle is the modern electronic enclosure: a goal that the company founder Kurt Hörburger already had in the 1970's. Now, with the help of these modern engineering tools it can finally be realized. Hörburger usually uses Rittal TS series enclosures – this gives the company an integration advantage, even for engineering. RiCAD 3D data by Rittal makes the design easier, plus the configurator "Rittal Therm" links via the EPLAN Data Portal. The total heat dissipation of the device projects can easily be calculated in the portal and transferred directly into the EPLAN project. Workflow is supported perfectly and continuously, all the way from design to production.
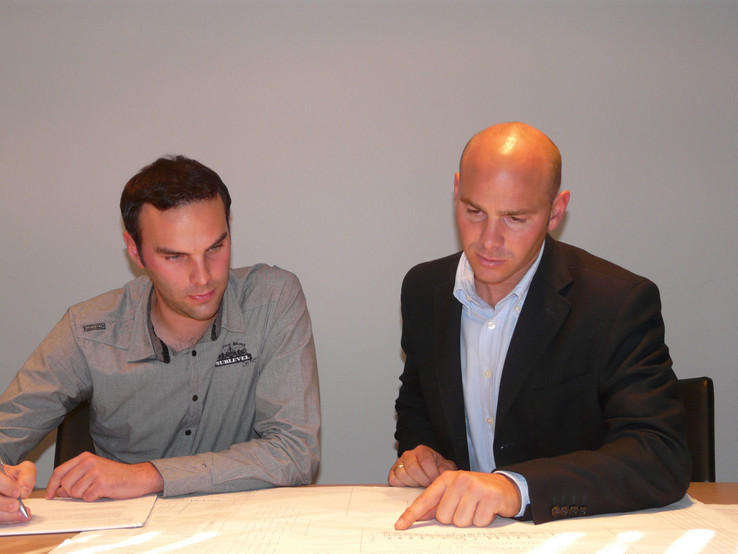
Hörburger AG consistently pursues the goal of simplifying the design of device automation. In the picture: chairman of the board, Dipl.-Ing. Christian Hörburger (to the right) in a discussion with Andreas Rusch, who developed the EEC based configurator.