Igniting the Automation Turbo
How can successful industrial companies further increase the throughput of their in-house production?
This was the question facing the Austrian company Hargassner. The leading provider of biomass heating systems is now manufacturing its own control cabinets with the maximum degree of automation along its entire value chain – thanks to software and hardware solutions from EPLAN and Rittal.
©Content: x-technik Verlag/Fachzeitschrift AUTOMATION

“Using EPLAN Smart Mounting and Smart Wiring, we can cover peak demand in production and also utilise less-skilled employees.”
Robert Burger, Electrical Workshop Director
A company that manufactures a majority of its products in house naturally has an interest in maximising its own production as far as possible. That is why Hargassner has been investing in automation at its headquarters and production facility in Weng, Austria for some time now – from robotics in sheet-metal processing to driverless transport systems in assembly. The easy-to-use operating software for its heating systems is also mainly developed on site.
The need – better software
Now it was time for Hargassner to invest more in its in-house control cabinet production, with the goal of increasing its independence and product quality. Having long manufactured the electrical portion only of its smaller heating systems, using outside firms to supply control cabinets for larger systems, the company made the decision to automate the construction of its electrical systems. Robert Burger, the director of Hargassner’s electrical workshop, explains: “We realised that we had to upgrade the software we were using for this because only with a digital twin would we be able to automate production to the extent we desired.” After a thorough market analysis, it was clear: “Only the combination of solutions from EPLAN and Rittal was able to fulfil our requirements.”
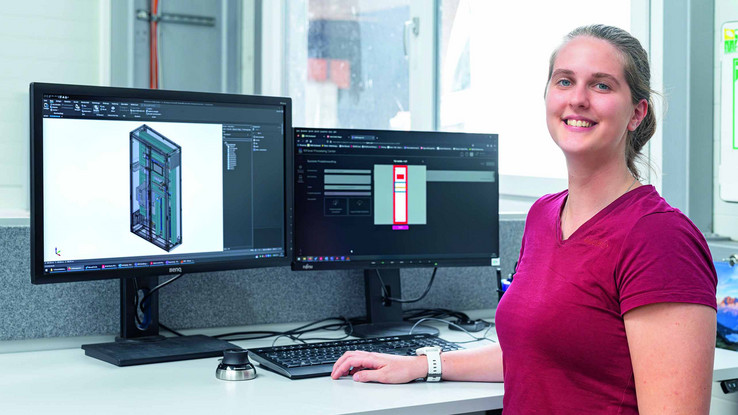
The digital twin of the control cabinet is created using EPLAN Pro Panel software, which includes all the information for downstream processes and provides it for each subsequent step.
The foundation – the digital twin
What was also clear was that creating the digital twin of a control cabinet required more than just the schematics. In addition to EPLAN Electric P8 design software, EPLAN Pro Panel was also needed to design control cabinets in 3D.
Today, design engineers at Hargassner use the 3D model of the installed components for the digital twin. Many of these components, including all Rittal products, are available in the manufacturer-independent EPLAN Data Portal. EPLAN Pro Panel can then be used to calculate all the required data, including the production data, based on the arrangement of the components and their connections. This includes deriving the programs for CNC milling systems and for cutting DIN rails and wire ducts to length, and naturally the information for the assembly of wire bundles and the like.
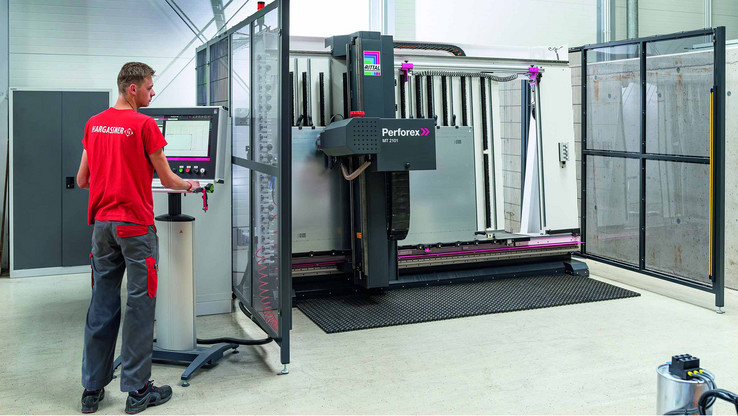
The Perforex Milling Terminal from Rittal enables the automated processing of control cabinet parts.
Data controlling machines
To wit, the Rittal Perforex Milling Terminal MT S takes the corresponding production data from EPLAN Pro Panel and, fully automatically, produces mounting plates, enclosure parts and doors with holes, threads and cut-outs as required. The system additionally uses Rittal’s RiPanel Processing Centre software to compare orders against material use.
The cutting centre Secarex AC 18 also works with data from EPLAN Pro Panel. It quickly and precisely cuts wiring ducts and their covers, not to mention mounting rails and busbars with the dimensions of NLS-CU 3/10. For labelling, a label printer is integrated into the machine. The Secarex AC 18 can also receive data directly from EPLAN Pro Panel. The system additionally offers cross-project waste optimisation.
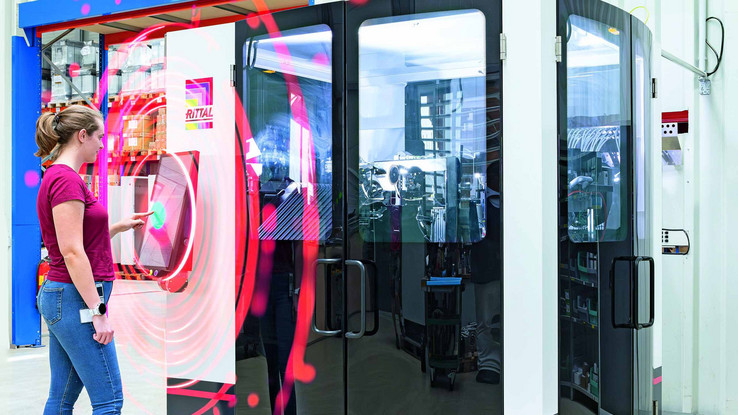
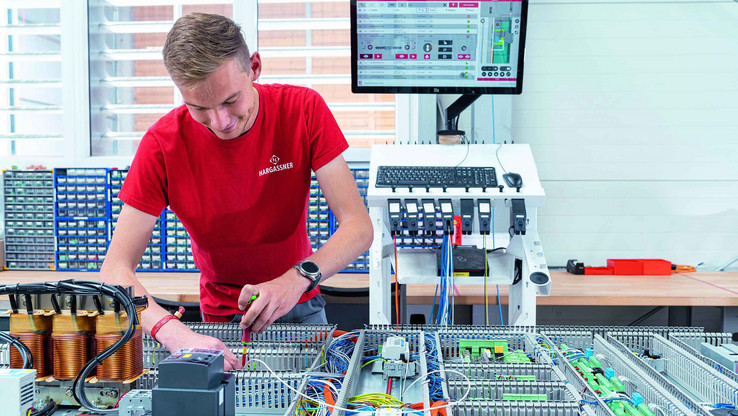
Every step in the wiring process is presented using clear visualisations in EPLAN Smart Wiring.
Assembly: the key to everything
The most important step in automating the production of control cabinets is wire assembly. Burger has been won over: “The ability to get wires of the right length as well as with the correct conductor termination processing and labelling – completely ready to be installed – saves time and reduces errors.” To achieve this Hargassner relies on the fully automatic Wire Terminal WT wire processing system from Rittal.
As a multifunctional processing unit, it carries out wire assembly from the reel up to ready-to-install elements. “The output in the form of wire bundles offers the ideal prerequisite for supplying our external production sites,” Burger is happy to report. “In addition to Rittal’s decision to involve us as a beta tester in the later development phase, this advantage accelerated our decision in favour of this investment.”
A wholly digital process
By combining hardware and software from EPLAN and Rittal, Hargassner has been able to develop a digital throughline for its processes. The data from EPLAN Electric P8 flows into the designs in EPLAN Pro Panel, where the digital twin of the control cabinet is created, providing the data that controls all the further steps in the process. The Perforex MT S produces the machined metal parts largely automatically, the Secarex AC 18 cutting system produces the busbars and wiring ducts, cut to length and labelled, and the Wire Terminal WT C produces the ready-to-install wire assemblies.
Yet the end of the control cabinet construction process hasn’t yet been reached. EPLAN Smart Mounting software supports Hargassner’s assembly technicians with precise specifications for the work steps, with full graphical visualisations for installing mounting rails, busbars and wiring ducts. The same applies to the wiring, which is carried out using EPLAN Smart Wiring software.
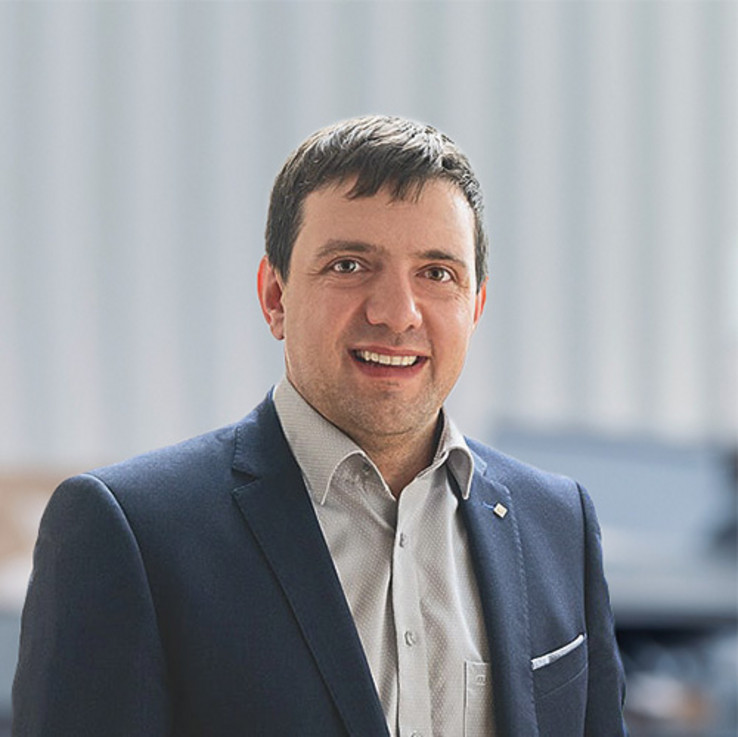
“The integrated, end-to-end solutions from EPLAN and Rittal enable us to achieve a high degree of automation that strengthens our global competitiveness.”
Anton Hargassner, Managing Partner
More quality, more flexibility
Burger is enthusiastic about these tools: “By insourcing with a high degree of automation, we not only have better control over availability and quality, but the EPLAN Smart Mounting and EPLAN Smart Wiring software tools also enable us to utilise employees who aren’t trained electricians to cover peak demands in production.”
The company’s Managing Partner Anton Hargassner is also impressed with the new overall solution: “The integrated, end-to-end solutions with EPLAN software and Rittal machines based on the digital twin enable control cabinet construction with a degree of automation that we are accustomed to from other areas of our production. The decision to adopt such a solution of this quality in-house strengthens our global competitiveness.”
Hargassner
Biomass is playing a central role in the energy system transition, especially in Austria. Almost half of the country is covered with forests, which is why one of the most important names in the production of sustainable heating systems is based there: Hargassner, headquartered in Weng, employs around 1,100 people and delivers more than 28,000 biomass heating systems – for wood chips, pellets, logs and combinations thereof – all over the world every year.